High quality spunbond non-woven
Spunbond non-woven fabric, the main material is polyester and polypropylene, high strength, high temperature resistance performance
Contents
1. spunbond non-woven Definition
Spunbond Nonwoven: After extruding and stretching the polymer to form continuous filaments, the filaments are laid into a web, and the web then undergoes its own bonding, thermal bonding,
chemical bonding or mechanical reinforcement methods to turn the web into a nonwoven fabric.
2. spunbond non-woven Features
Good high temperature resistance, good low temperature resistance (polypropylene can be used in 150℃ environment for a long time,
polyester can be used in 260℃ environment for a long time), aging resistance, UV resistance, high elongation, good stability and air permeability, corrosion resistance, sound insulation, anti-moth, non-toxic.
3. spunbond non-woven Main uses
The main materials of high quality spun bond non-woven fabrics are polyester and polypropylene.
The main products of spun bond non-woven fabric are polypropylene, polyester (long fiber, staple fiber) non-woven fabric, our most common and most commonly used applications are non-woven bags, non-woven packaging, etc.;
for spun bond non-woven fabric is easier to identify, the general two-way fastness is good, and the rolling point of general spun bond non-woven fabric is diamond-shaped.
The level of application can also do flower packaging cloth, bag cloth, etc. The characteristics of abrasion resistance, firm hand feel, etc. make him the best choice for making such products.
4.spunbond non-woven Process flow
Polypropylene: polymer (polypropylene + back) – large screw high temperature melt extrusion – filter – metering pump (quantitative conveying) – spinning (spinning inlet up and down stretch
pumping) – cooling – airflow traction – net curtain into a network – upper and lower pressure rollers (per-reinforcement) – mill hot rolling (reinforcement) – winding – rewinding slitting – weighing and packaging – finished products into storage
Polyester: processed polyester chips – large spiral high temperature melt extrusion – filter – metering pump (quantitative conveying) – spinning (spinning inlet up and down stretch suction) –
cooling – airflow traction – net curtain into a network – upper and lower pressure rollers (pre-reinforcement) – mill hot rolling (reinforcement) – winding – rewinding and slitting – weighing and packaging – finished products into the warehouse
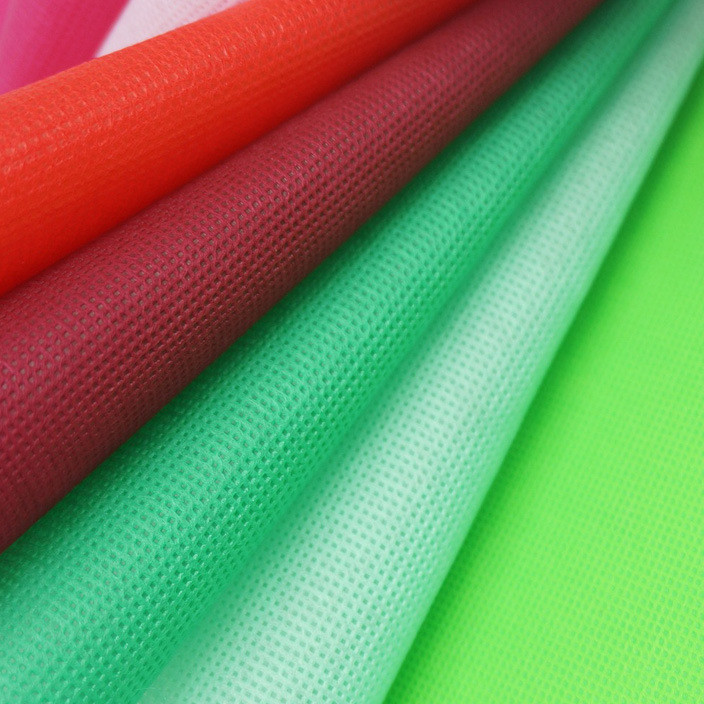
5.spunbond non-woven Technology type
The main spun bond non-woven technologies in the world are Reconcile technology from Germany, TSP technology from Italy, and Kobe Steel technology from Japan. The current situation,
especially with the Le fen technology has become the mainstream technology in the world.
It has been developed to the fourth generation technology.
Characterized by the use of negative pressure ultra-high-speed air drawing, the fiber can be stretched to about 1 denier.
There are many domestic enterprises have been copied, because its core technology has many cutting-edge problems have not been solved or mastered, domestic equipment manufacturing enterprises to reach the level of Lenin technology is still waiting for time.
6. Advantages of ET spunbond nonwoven fabric.
1, the product gram mage scale wide. PET spun bond method spinning selection of positive pressure drafting, the production of non wov en gram mage scale up to 15 ~ 240 g/m2,
PET spun bond hot-rolled cloth gram mage in 15 ~ 255 g/m 2 or so, PET spun bond needle punching cloth in 130 ~ 600 g/m2.
and general domestic imitation Lenin 2 PP spun bond non woven production line, because the use of negative pressure drafting, with fans in The thick products will lead to the lack of initial fiber drafting,
and thus cannot produce products of 120 g/m 2 or more. Now Lenin 3 and 4 have increased the positive pressure drafting equipment, the gram mage scale of the products produced will be improved.
2, production process adjustment flexibility. the PET spun bond production line of the spinning box selection of multiple independent metering pumps for melt metering,
each metering pump supply melt to the regular number of spinning components, so production can be based on customer orders, stop / open a single metering pump, and then swing the silk stopper adjustment,
you can produce different widths of semi-finished products, width adjustment in the 2.0 ~ 3.4 m between.
In addition, in the semi-finished products in some aspects of the target is not up to standard, can replace the corresponding spinning components to adjust, such as air permeability can not, can replace a spinneret holes less spinning components to increase the air permeability of the fabric.
PP spun bond method generally uses the whole spinneret spinning, the production process can not adjust the width, resulting in too much edge material to form a waste. And the production of the product target is not uniform, the adjustment method monotonous.
3, the product lateral strength is large. PET spun bond method uses the pendulum into the mesh method into the network.
Pendulum in 750 Hz frequency to swing back and forth, through the high-speed drafting of the fiber transversely into the net curtain, because into the net curtain forward movement, so that the fiber oblique interlaced with each other,
so PET spun bonded fabric strength is large, longitudinal strength ratio can basically reach 1:1. PP spun bonded general choice of venture chaotic, general strength is not high, longitudinal strength ratio is large.
4, PET fiber high temperature resistance, good wear resistance, mechanical strength than PP fiber.
Defects of PET spun bond non-woven.
1, high energy consumption.
PET slices have to be crystallized and dried before they can be fed into the screw machine, while PP slices can be directly fed into the screw machine.
If you need to participate in large quantities of additives, you also need a small set of crystallization and drying system for additive drying.
In addition, our factory specializing in the production of thin products production line selection of double box equipment, that is, the use of two sets of screw extruder,
two sets of spinning box and two sets of swing into the network (in order to better product uniformity), the production of the same gram of products than PP spun bond energy consumption more. But the big power eater is still the compressor that provides the compressed gas for positive pressure drafting.
Our company uses a total of 15 U.S. Should air compressor, a 3000 Kw (specific forget), basically 60% of the plant’s electricity consumption are in these compressors.
Because the draft air pressure is large, so the suction of the wind under the corresponding increase in suction volume, how much did not see, but I stand in the lower suction air outlet, feel like a 10-step hurricane blowing over, people can not stand.
2, raw material waste. Semi-finished products cut out of the trim is not recyclable, can only be sold as scrap.
Our factory spent hundreds of thousands of dollars to buy a granulation, the trimmings, waste cloth re-granulation, the result of a serious decline in molecular weight, mixed to the new slices production, spinning is extremely unstable,
only open for a week has been abandoned. In addition, PET in the spinning component extrusion, there will be a very small amount of volatile differentiation, pollution spinneret plate surface, we generally in 2 ~ 3 days will be set to sort out the spinning plate surface (we call the set shovel plate). Set shovel plate is still continue under the silk, according to the shovel plate speed,
out of the waste cloth waste silk in 200 ~ 500 kg, only when the waste cloth processing.
And PP spun bond trim can be directly used a chemical fiber extrude melt, and screw extrude melt mixing out, trim recovery rate is high.
3, to time the quality of the cloth surface. Spinning component of the spinneret pollution, external leakage, etc. will form dripping pulp, stiff silk.
Because PET spinning viscous is open spinning (that is, the silk strip exposed to the top of the air with side blowing wind cooling), the environmental airflow will change the General Assembly to form bleached silk,
broken head, through the drafting tube will lead to some silk hanging on the pendulum piece, other silk entangled to a piece of the fabric surface to form and silk, hard blocks, etc..
If it is some group head silk also need to replace the components.